I spend half the day getting the twist out of my lathe bed so there is no taper on turned parts unless taper is wanted. Thought that the 12" thick pad of reinforced high strength concrete would have been stable enough. I though wrong. Graziano SAG12 manual recommended 18" thick pad under the lathe. Perhaps after a couple of years one should expect some settling and also had a small earthquake today. First thing to getting the twist out of the bed was to level the lathe using a Hilger &Watts precision level with 0.00025IN in 10IN per DIV. Leveling does not guarantee the bed twist is gone but is rather just a starting point. Next I mounted a 2.75" 1/4" wall aluminum tube in a 3-jaw chuck and turned the tube with 3/8" wide lands 7" apart. I used a successive approximation algorithm to turn the lands, measure the diameter difference with a 2-3" micrometer, adjust one of the four level screws that support the lathe, and re-measure and repeat the procedure until the difference was as small as I was willing to deal with which was about 0.0001". Turns out repeatable measuring "tenths" using a micrometer took some time for me to develop and a tenth of a mil was pretty difficult to master. This lathe is very beefy weighing 2200 lbs and today have had a real experience in the lack stiffness in what appears to be absolutely rigid material (cast iron).
Turning 2.75" diameter x 10" long test gage. Note: carriage way guards were removed for using a level on the ways.
![]()
Measuring diameter difference using 2-3" micrometer
![]()
![]()
Turning 2.75" diameter x 10" long test gage. Note: carriage way guards were removed for using a level on the ways.
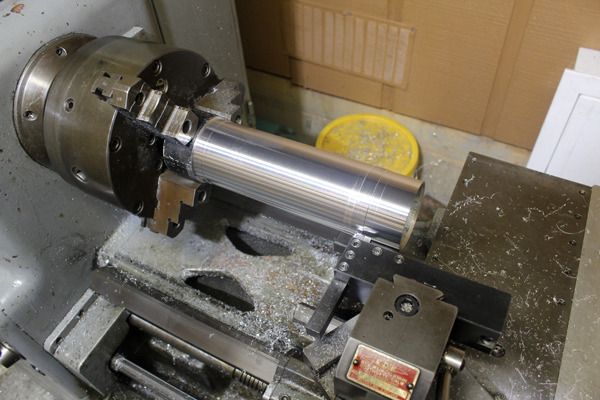
Measuring diameter difference using 2-3" micrometer
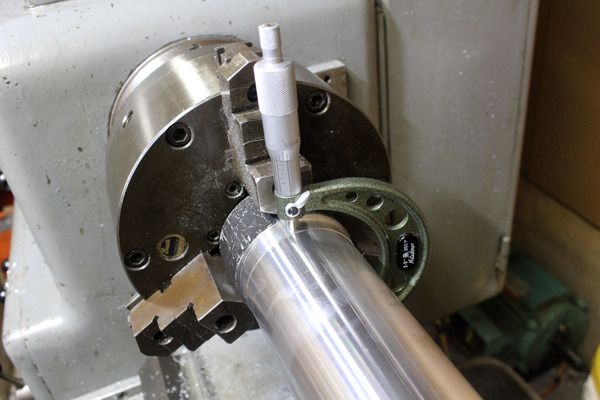
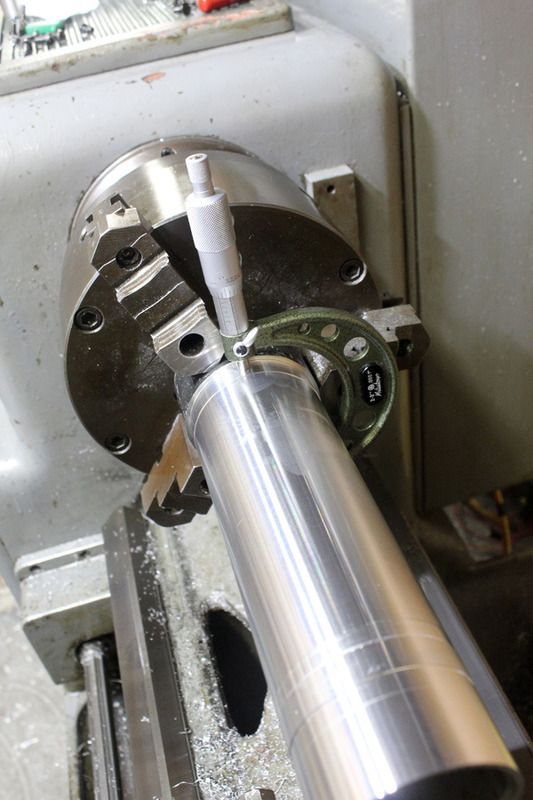